Production (Low Risk)
Bottling, packing and labelling processes are lower risk areas where lighting is concerned. The food product is now sealed up or within pressurized & sealed production equipment, thus the outside environment is less critical regards cleanliness, although lower pressure wipedowns are still commonplace.
Complex conveyor systems and large automated machinery often create dark areas which must be appropriately accomodated for. Further production areas often require maintained traffic routes for pallet loaders and other hand driven machinery.
24hr operation is usual and any machine downtime is critical, most productions sites have on site maintenance workshops, usually quite close to the production lines.
For recommended lux levels please see CIBSE : SLL Lighting Guide 1 - The Industrial Environment (2012, updated 2018)
Illumination Levels
The requirements will vary depending upon the industry, but typical values are 200 - 300 lux in automated process areas, 300 - 500 lux where manual operations take place and 500 - 750 lux in inspection areas.
The CIBSE: SLL Lighting Guide 1 - Industrial Environment 2018 provides guidance for specific industries and processes, although many companies have their own engineering standards.
Application | Minimum maintained mean illuminance (lux) | Illuminance uniformity (minimum/average) |
---|---|---|
Labelling and packing | 300 | 0.60 |
Bottle filling | 500 | 0.60 |
Thorlux Recommends
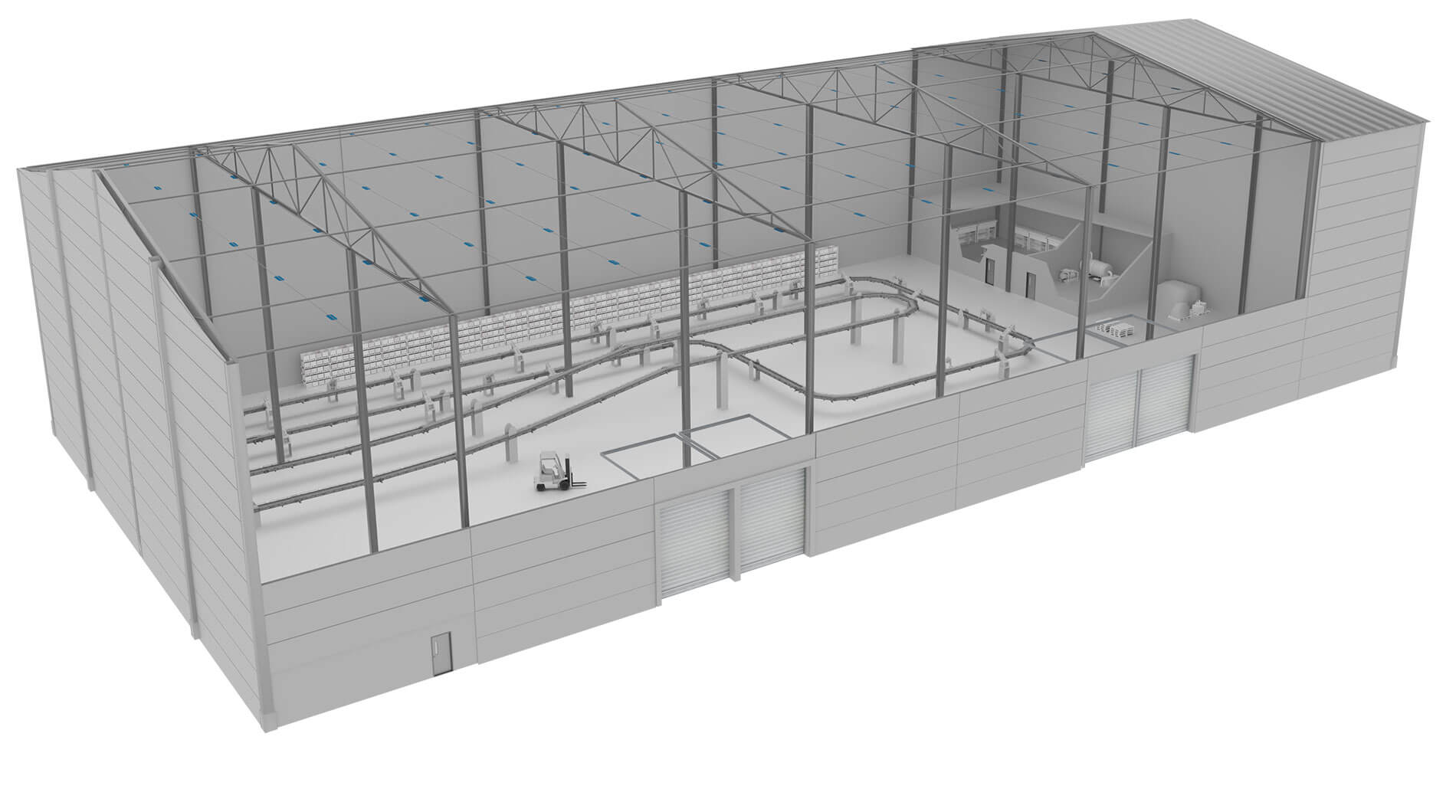